Seeking new ways to improve without losing what one has.
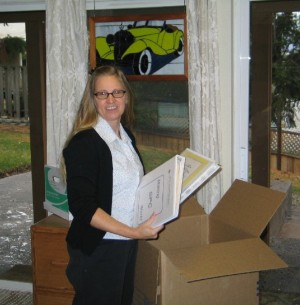
We’ve been thinking a lot lately about “driving change”. Not just because our own move created many changes that required and still require real effort to make changes for the better. We have also seen over the last decade the difficulties of the process our clients go through to shape the type of environment where dramatic, progressive change and innovation can occur.
Unfortunately gone are the days when success was assured just by doing something the way you’ve always done it. Today’s rules are different. Companies must be more concerned about what changes they can make to keep their customers happy and satisfied. To venture beyond what one knows and feels comfortable with can be daunting. It takes progressive change, and that is not an easy accomplishment.
Lean Manufacturing is touted in some corners as the “quick solution”. The idea is that by adapting lean initiatives, companies can eliminate waste and make perfect parts all the time, and do so really, really fast. It makes it sound simple, just an extension of what one already does, and on one level that is not far off. We say that because we have seen and contributed to that happening, but we also know that it is not so simple, because in manufacturing we don’t work in a perfect world. If you set out with a mindset that perfect conditions lie just around the corner, you likely will never find that turnoff.
Yes, we at AEM Consulting believe that lean manufacturing can achieve incredible returns, but it has to be approached in the proper mindset. One must understand that revising the culture of an organization to a progressive change environment is not a small feat. It evades many talented folks.
We’ve found three key considerations necessary for implementing progressive change:
- Real change is driven from the top down. If the person at the top is not truly committed to the change, it is very unlikely to happen.
- People will resist, maybe passively or actively. It’s not enough to have a few people on board – the whole team must be involved. Facilitating groups of people is not an easy task. You’ve got to be a coach, administrator, teacher, manager, cheerleader and problem-solver all rolled into one.
- It isn’t sufficient to experiment in one small area; dramatic change must become a way of doing business. Continuous improvement does not have an ending.
Are the above hurdles worth jumping? If the goal is to have a more successful, profitable operation, we think so. We also believe the hurdles are able to be cleared.
By AEM Consulting Group, Inc.